Laser Cleaning in the Application of New Energy Lithium Battery Industry
Mainly Contains the Following Three Applications,
- Lithium Battery Core Lug Piece Welding
- Electrode Pieces of Lithium Batteries
- Lithium Battery Cell Overwrap Film
Electric Vehicles to Promote the Rapid Development of the Lithium Battery Industry, So the Big Market Was Created That to Use Laser Cleaning Technology in Lithium Batteries Production Processses.
The Production of Lithium Batteries is a “roll-to-roll” Process, Whether It is Lithium Iron Phosphate Batteries, Sodium-Ion Batteries or Ternary Batteries Need to Go Through the Process from Thin Film to Individual Cells, and then into a Battery System. the Preparation Process of Lithium Batteries Can Be Roughly Divided into Electrode Sheet Production, Cell Synthesis, Packaging into Three Sections.
In These Three Major Processes, There Are Several Key Processes, Which Will Directly Affect the Battery’s Storage Capacity, Product Safety, and Service Life. Therefore, Different Production Processes Output Battery Performance Varies Greatly. in These Links, Laser Cleaning Machine Can Now Participate in More Than a Dozen Items of the Preparation Process, which Can Significantly Improve the Rate of Lithium Battery Quality.
Laser Cleaning of Copper or Aluminum Electrode Sheets Before Coating of Battery Electrodes
The Positive and Negative Electrodes of Lithium Batteries Are Made by Coating the Positive and Negative Materials of Lithium Batteries on Aluminum Foil and Copper Foil, and the Electrode Coating is Important for the Safety of the Batteries. The Coating Process Can Cause Micro-short Circuit Inside the Battery if Particles, Debris, Dust and Other Media Are Mixed In, Which Can Lead to Fire and Explosion in Serious Cases.
Therefore, the Foil Needs to Be Cleaned Before Coating to Obtain a Completely Clean and Oxide Free Surface. MOZLASER Laser Cleaner is a Very Suitable Option for Cleaning These Electrode Foils.
Laser Cleaning, As a Dry, Non-consumable Cleaning Method, is Close to Zero Defect in Terms of Cleanliness and Hydrophobicity of the Aluminum Foil Surface Treatment, Which Ensures the Maximum Effect of Sizing and Coating of the Pole Piece.
The Use of Laser Cleaning of Metal Foil Not Only Improves the Efficiency of the Cleaning Process and Saves Cleaning Resources, but Also Establishes Real-time Monitoring of the Cleaning Process Data and Quantitative Determination of the Cleaning Results, Which Can Effectively Improve the Consistency of the Batch Production of Electrode Sheets.
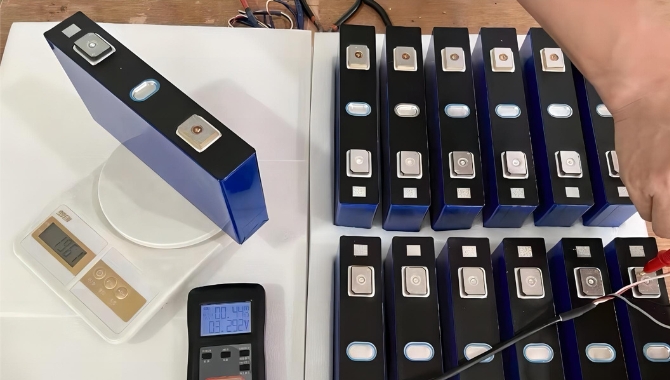
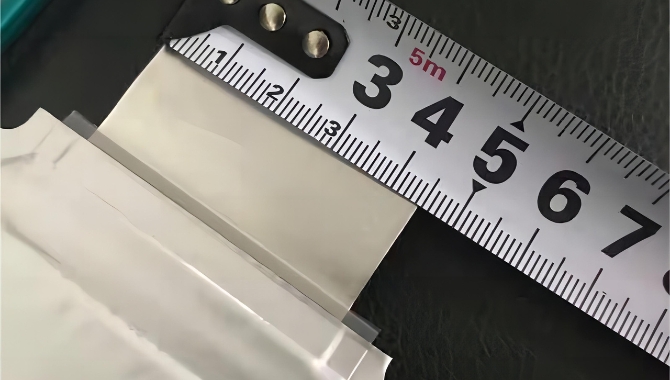
Laser Cleaning Before Welding the Lithium Battery Lugs
The Lugs Are the Metal Strips That Lead from the Positive and Negative Electrodes in the Cell and Are the Contact Points when the Battery is Charged and Discharged. Contaminants on the Surface Such As Grease, Corrosion Inhibitors, and Other Compounds in the Process Can Lead to Poor Fusion, Cracks, and Porosity at the Weld.
During the Factory Process, the Lugs Are Often Uneven, Bent, or Even Twisted, and the Strength of the Lug-cell Weld is Weak, Making False Welds, Fake Welds, and Short Joints when Welding, Resulting in Lower Conductivity of the Welded Joint and Ultimately Limiting the Overall Performance of the Battery Pack.
The Cleanliness of This Contact Point Surface Can Greatly Affect the Reliability And Durability of the Electrical Connection. Laser Cleaning Machine Can Effectively Remove Dirt, Dust, Etc. from the End Surfaces of the Cell Poles and Prepare the Cells for Welding in Advance.
Because MOZLASER Laser Cleaner Does Not Require Any Consumables Such As Solid-liquid-gas, Has a Compact Structure, Takes Up Little Space, and Has Significant Cleaning Effects, It Can Significantly Increase Production Turnaround and Reduce Manufacturing Costs. It Can Roughen the Welding Surface on the Basis of the Thorough Removal of Organic Matter and Tiny Particles, and Improve the Reliability of Subsequent Laser Welding. Laser Cleaning Technology is one of the Best Choices for Lithium Battery Pole Ear Cleaning.
Laser Cleaning of the Outer Envelope of the Lithium Battery During Assembly
In Order to Prevent Safety Accidents of Lithium Batteries, Generally Need to Be Outside the Lithium Battery Cell Adhesive Processing, in Order to Play the Role of Insulation, to Prevent the Occurrence of Short Circuits As Well As to Protect the Line, to Prevent Scratches.
At Present, Many Domestic Battery Companies Still Rely on Manual or Less Automated Processes to Complete This Link, Mostly Just a Simple Wrapping Operation, Which is Inefficient and Costly. There is No Effective and Comprehensive Cleaning of the Battery Case Before Wrapping, and There is No Precise Testing of the Effect After Wrapping.
When CCD Inspection is Performed on the Outer Wrapping Film of Not Thoroughly Cleaned Cells, the Appearance Will Have Bad Conditions Such As Folds, Bubbles, and Scratches, and Bubbles with a Diameter of ≥0.3mm Can Often Be Detected. There is a Probability of Leakage and Water Rust Corrosion, Reducing the Life of the Battery While There Are Also Safety Risks.
Laser Cleaning Can Reach Sa3 Level on the Surface Cleanliness of the Battery Cell, with a Removal Rate of More Than 99.9%, and There is No Stress Effect on the Surface of the Battery Cell. Compared with Other Cleaning Methods Such As Ultrasonic Cleaning or Mechanical Polishing. Laser Cleaning Machine Can Ensure the Maximum Degree of Physical and Chemical Indicators Such As the Hardness of the Cell Surface Does Not Change and Prolong the Service Life of the Battery.
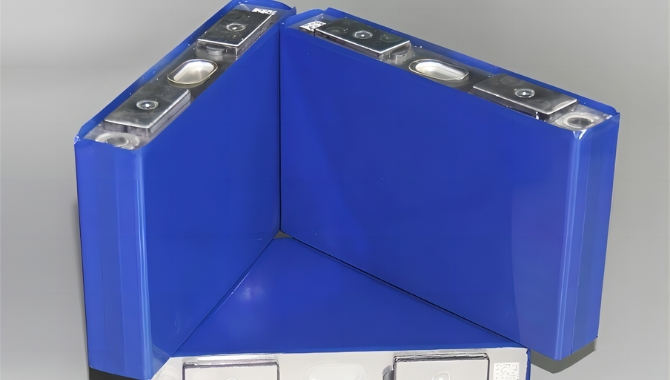
The Advantages of Laser Cleaning Compared to Traditional Ultrasonic Cleaning, Chemical Cleaning, Plasma Cleaning in the Lithium Battery Industry.
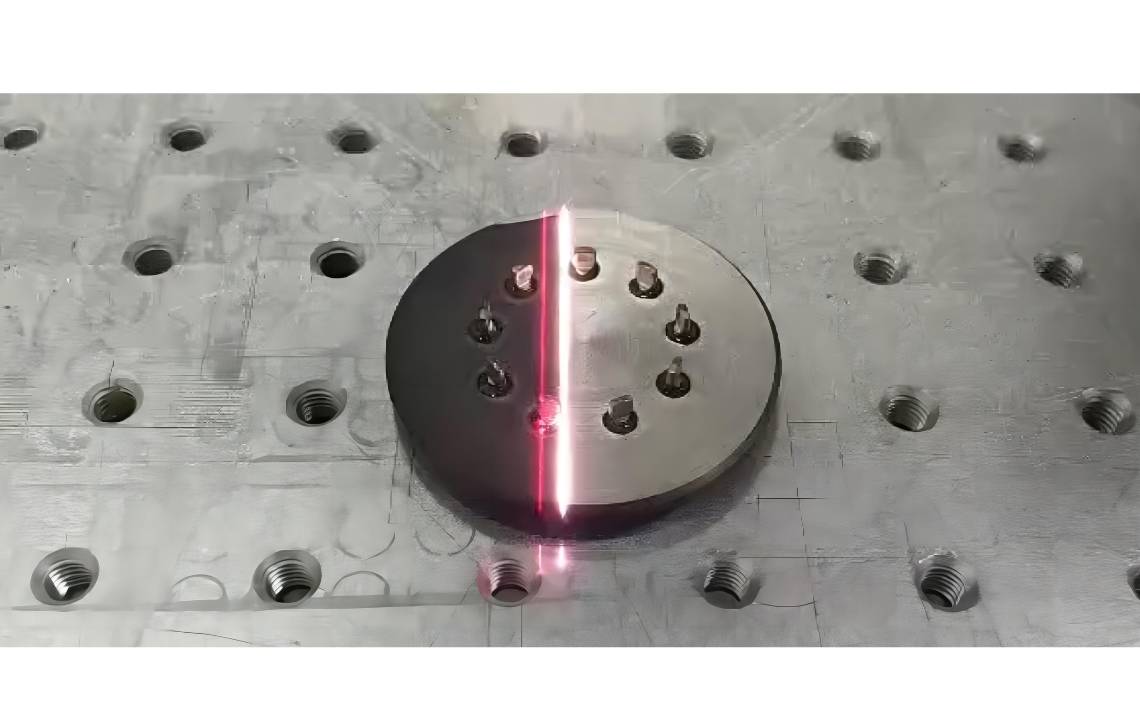
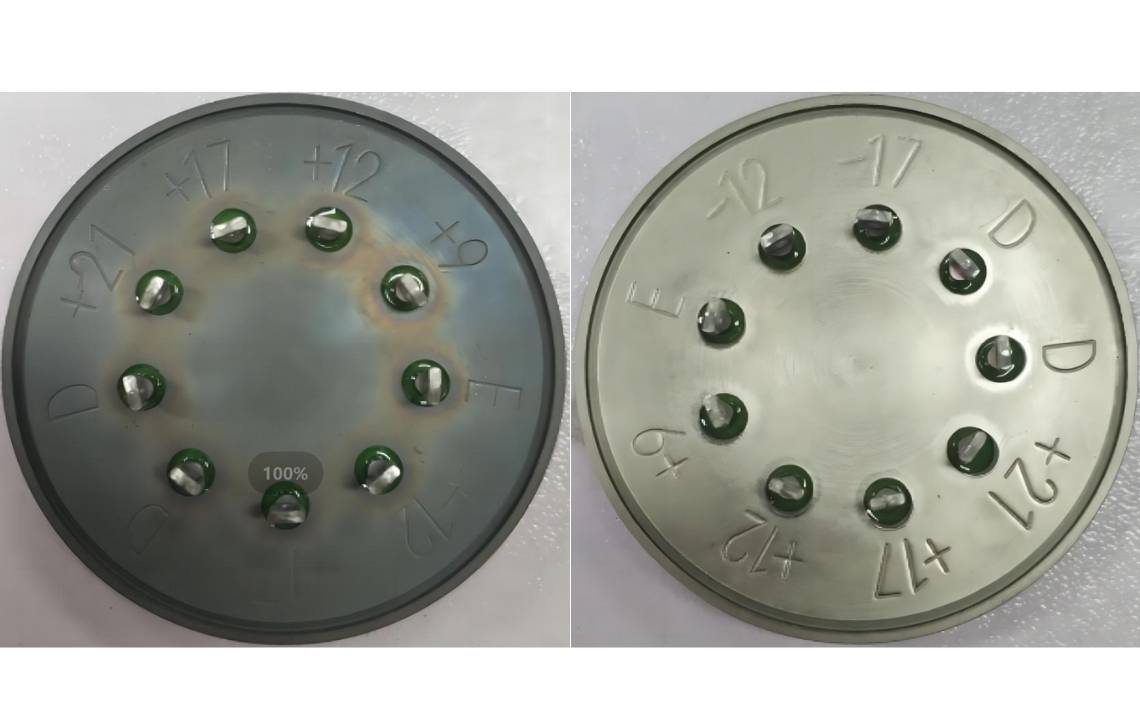
Traditional Cleaning Lithium Battery Electrode Sheet Generally Uses Ultrasonic Cleaning, with Ethanol Solution As a Cleaning Agent In a Pre-coating Cleaning Process. the Above Way Has the Following Defects.
1. Ultrasonic Cleaning Metal Foil Parts, Especially Aluminum Alloy Workpieces, by the Frequency, Cleaning Time, and Power, the Cavitation Effect of Ultrasound is Easy to Corrode the Aluminum Foil, Resulting in Fine Small Holes, the Longer the Action Time, the Larger the Small Holes. and Lithium Battery Foil Used in the Foil is Generally a Single Zero Foil with, a Thickness of 10 μm, More Susceptible to Tearing into Holes Due to Cleaning Process Problems.
2. Using Ethanol Solution As a Cleaning Agent Not Only Easy to Cause Damage to Other Parts of the Lithium Battery but Also Easy to Appear “hydrogen Embrittlement” Phenomenon, Affecting the Mechanical Properties of the Aluminum Foil Index.
3. Although the Cleaning Effect is Better Than Traditional Wet Chemical Cleaning, the Cleanliness is Still Not As Good As Laser Cleaning, the Surface May Still Occasionally Exist Contaminants, Resulting in Coating and Foil or Produce Shrinkage.
Laser Cleaning As a Dry Non-consumable Cleaning, in the Surface Treatment of Aluminum Foil Cleanliness and Hydrophobicity and Other Indicators, Are Close to Zero Defects, the Maximum Degree to Ensure the Effect of the Pole Sheet Sizing Coating.
The Existing Lithium Battery Lug Cleaning Mostly Uses Manual Cleaning, Wet Chemical Cleaning, or Plasma Cleaning,
1. Manual Cleaning is Inefficient and Costly.
2. Wet Flow Cleaning Line Although the Efficiency is Improved, the Length of the Line is Long, Occupying a Large Area of the Factory, and the Chemical Agent Also Easy to Damage Other Lithium Parts.
3. Plasma Cleaning Although No Liquid Medium, but Also Need Process Gas As Consumables and Gas Ionization Will Lead to the Positive and Negative Electrodes of the Battery being Easy to Conduct, the Application Often Has to Flip the Cell Several Times to Clean the Positive and Negative Electrode Lugs Separately, the Actual Efficiency is Not High.
Laser Cleaning Machine Can Roughen the Welding Surface on the Basis of Thorough Removal of Organic Matter and Tiny Particles, and Improve the Reliability of Subsequent Laser Welding. It is one of the Best Choices for Lithium Battery Lug Cleaning.